IL PROGETTO |
Parte fondamentale ed appassionante del nostro lavoro
è il progetto vertigo, attualmente in fase di sviluppo.
La sfida che ci siamo posti è di portare il concetto
dell’aereo canard nel nuovo millennio, cioè applicare lo stato
dell’arte della tecnologia dei materiali compositi alla costruzione di
un progetto molto affascinante seppur datato: l’aereo canard Rutan
derivato(in foto un molto particolare Rutan Long-Ez). |
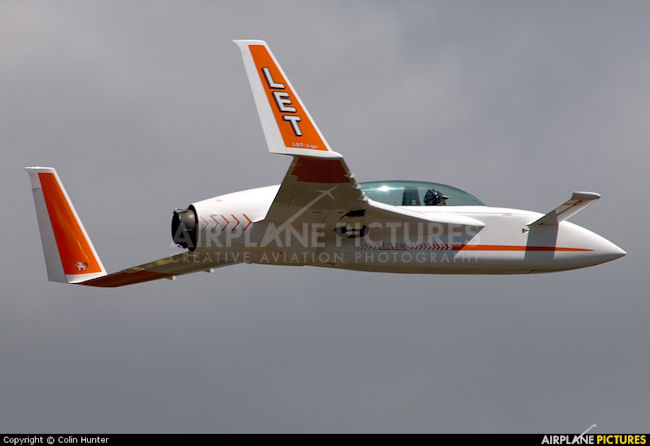 |
In principio questo tipo di velivolo veniva(metodo tuttora
utilizzato) costruito assemblando pannelli sandwich di fibra di
vetro laminata a temperatura ambiente con stratificazione manuale
su schiuma di pvc. Sebbene questo metodo costruttivo sia stato uno
dei punti di forza del progetto Rutan che lo ha reso forse il
rappresentante più numeroso nel mondo dell’autocostruito, è con il
passare del tempo divenuto uno dei suoi limiti. In un tempo in cui
la tecnologia del composito si limitava al vetro impregnato
manualmente, la velocità e la semplicità costruttiva unite alle
sorprendenti caratteristiche meccaniche del manufatto(oltre
ovviamente alle caratteristiche di volo e al look affascinante) ne
hanno decretato il successo fra gli appassionati autocostruttori
ma con l’avanzare della tecnologia in ambito dei materiali
compositi i limiti di questo progetto si sono evidenziati sempre
di più.
Negli anni ‘90 grazie al diffondersi della tecnica di
laminazione sottovuoto comparve l’agguerrito Berkut, discendente
diretto del già assai performante progetto Rutan. |
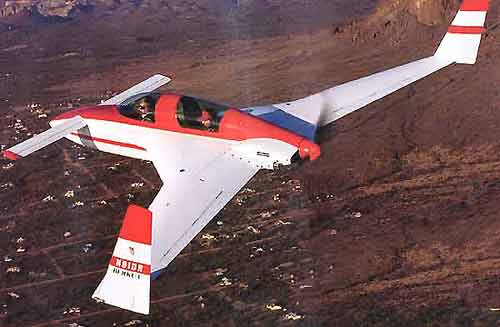 |
A differenza del suo predecessore Long-Ez, il Berkut, abbandonata
la tecnica moldless(mantenuta solo per la costruzione delle
superfici aerodinamiche) era costruito in stampo sottovuoto e
vedeva comparire la fibra di carbonio nei longheroni alari.
Il divario generazionale in termini di prestazioni fra i due
velivoli è molto consistente.
Nonostante la fusoliera fosse costruita di stampo, il Berkut
manteneva le forme squadrate imposte dalla costruzione moldless
del suo progenitore Long-Ez, di cui sotto possiamo vedere
evidenziati i punti di maggior resistenza aerodinamica in
corrispondenza del muso, della parte frontale della cappotta,
della cofanatura motore e anche in corrispondenza della radice del
canard. |
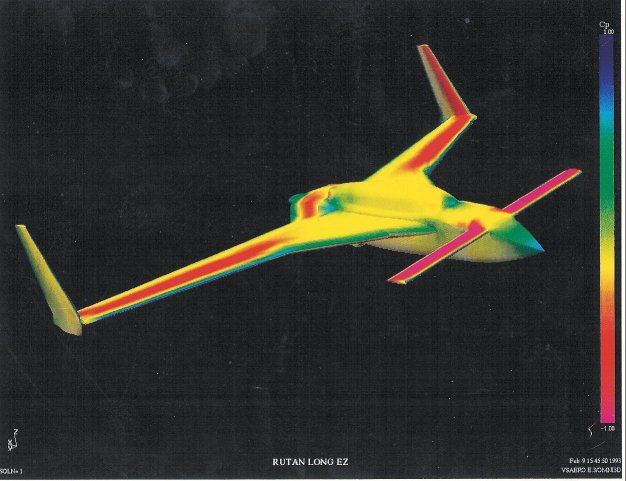 |
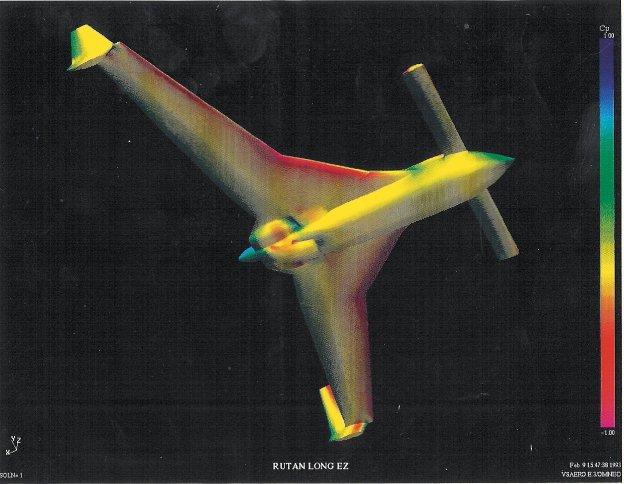 |
L’ambizione del progetto Vertigo è quella di inserirsi in questo
punto della storia.
Vertigo
è un velivolo realizzato interamente in carbonio prepreg curato in
autoclave ad alta temperatura e pressione, all’interno delle
strutture sandwich il pvc ha lasciato il posto al nomex e benché i
profili aerodinamici e la loro posizione rimanga invariata, la
forma della fusoliera non più legata al concetto di moldless è
adesso libera di essere quello che noi qui alla Vertigo Aerospace
siamo convinti fosse l’idea iniziale di Rutan. Le forme sono state
armonizzate, tutte le intersezioni raccordate e la linea è ora
davvero fluente(il rendering qui sotto mostra l’intersezione ala/winglet
tradizionale anziché la configurazione blended winglets che invece
verrà adottata per migliorare le performances di quella zona
aerodinamica). |
 |
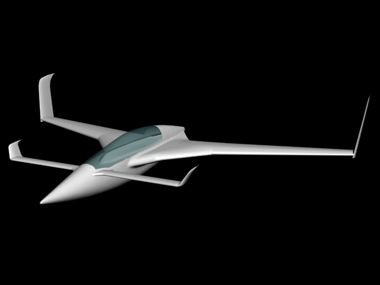 |
Non è difficile pensare che l’idea del geniale
Burt fosse stata quella di realizzare una fusoliera filante ed
arrotondata simile a quella di un’aliante, come del resto la fibra
di vetro e le resine gli avrebbero consentito di fare, ma al
pesante costo di costruire da stampo ogni componente: per far
questo avrebbe dovuto costruire egli stesso le parti dell’aereo e
venderle poi come kit. La sua geniale intuizione invece fu proprio
quella di mettere in condizione ogni autocostruttore di realizzare
in proprio tutte le parti dell’aereo, potendo anche
personalizzarle in una certa misura, minimizzando così gli
investimenti sia per se stesso che per l’homebuilder.
Benché ancora oggi il Long-Ez venga costruito come una volta(moldless)
e diverse varianti al progetto siano disponibili, la
tecnologia ai nostri tempi disponibile rende assurdo ai nostri
occhi continuare sulla stessa strada e crediamo che l’unica ragion
d’essere di una costruzione moldless possa essere oggi, a parte il
costo esiguo, la volontà di onorare un progetto intramontabile e
la passione per quel gusto un po’ retrò.
Qui alla Vertigo Aerospace ci siamo posti l’obiettivo di
rendere disponibile al pubblico un velivolo altamente raffinato,
dalla linea molto aggressiva, costruito con le migliori tecnologie
dei materiali compositi, dall’altissimo standard di affidabilità e
dalle altissime prestazioni: in poche parole “il canard allo stato
dell’arte”. |
IL PROCESSO PRODUTTIVO |
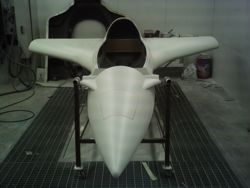 |
Parlando di una costruzione da stampo, la prima cosa
necessaria è stata costruire un modello di partenza dal quale
sarebbe poi nato lo stampo(in foto il moke-up della
fusoliera). Partendo dalle dimensioni originali del progetto
Rutan abbiamo costruito un moke-up rivisto nell’abitabilità e
nel comfort, in considerazione delle accresciute dimensioni
del corpo umano dagli anni ‘80 ad oggi. |

Sulla base di questa semplice struttura(in
foto la simulazione delle dimensioni interne di un Long-Ez) è
stata creata la forma finale, mantenendo inalterata la
posizione delle superfici aerodinamiche e del propulsore così
da rispettare i centraggi del progetto originale.
Per poter fare un passo avanti rispetto alle costruzioni
moldless e standardizzare il prodotto in un kit dalla qualità
indiscutibile il moke-up della fusoliera è stato sottoposto ad
un analisi di standard deviation. |
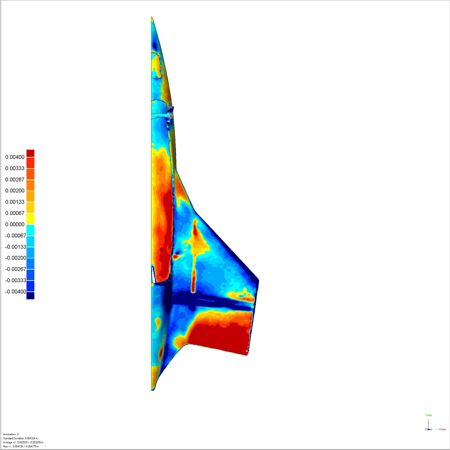 |
|
La matematica dell’oggetto è stata acquisita
tramite una scansione laser ed importata in un programma di
modellazione tramite il quale è stato possibile tagliarla a metà
in senso longitudinale, specchiarla e sovrapporre la parte destra
sulla sinistra in modo da evidenziare eventuali scostamenti dalla
linea di simmetria.
L’immagine a fianco è un’esempio intuitivo che dimostra quanto
detto prima:
tale tecnica permette di evidenziare i punti che si discostano
dal piano di simmetria con una precisione che ha
dell’incredibile(i diversi colori indicano gli scostamenti
dimensionali fra le due metà sovrapposte).
Avendo chiara l’entità degli scostamenti dalla forma voluta,
la fusoliera è stata poi sezionata virtualmente in una serie di
fette ad una distanza di 5 cm l’una dall’altra per tutta la sua
lunghezza(foto a sinistra) generando così una serie di dime
realizzate in acciaio tagliato a laser che una volta appoggiate
sul moke-up hanno reso possibile la correzione degli errori in
maniera semplice e veloce(nella foto a destra alcune delle dime
usate per la correzione). |
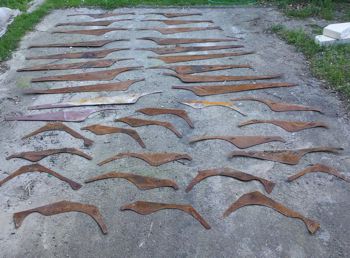 |
Una volta portato a termine il lavoro di
correzione di forma(nell’ordine di errore < di 0,2 mm) è iniziato
il processo di costruzione dello stampo.
La tecnica scelta per tale processo è la vacuum infusion. Con
tale processo si ottiene un prodotto esente da difetti e di
altissima qualità. |
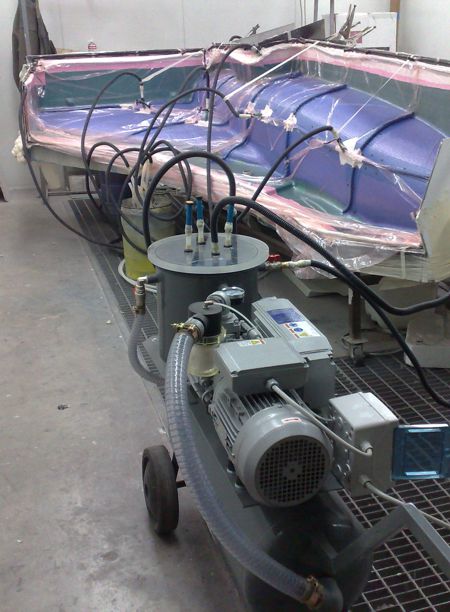 |
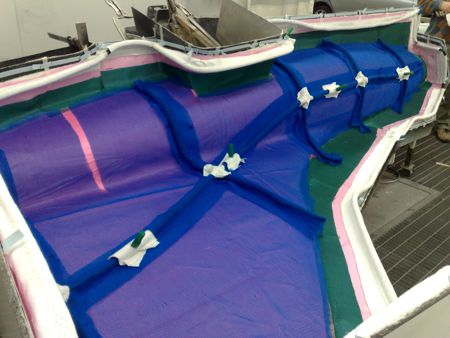 |
nelle foto sopra si può avere un’idea del
processo di vacuum infusion: tutto l’oggetto viene messo in un
sacco a vuoto e portato dalla pompa(foto a sx) ad una pressione di
-0,9 bar, aprendo poi la mandata di resina, questa
viene risucchiata direttamente dalla forza del vuoto dentro al
sacco attraverso i canali visibili in foto a dx e distribuita su
tutta la superficie dello stampo dalla rete azzurra che serve
appositamente a veicolare la resina su tutto il tessuto che la
riceve ad effetto “pioggia”.
Lo stampo realizzato per infusione, prodotto molto compatto,
esente da vuoti e bolle d’aria viene poi postcurato ad alta
temperatura per essere processato in autoclave. |
 |
A fianco la parte superiore dello stampo appena
staccata dal moke-up ed ancora bagnata dopo il lavaggio del
distaccante polivinilico, in attesa del processo di lucidatura.
Una volta preparato lo stampo, lucidato, postcurato e trattato
con distaccante chimico semipermanente moldrelease(non si usano
ASSOLUTAMENTE MAI distaccanti a base cerosa per non contaminare il
manufatto).
Inizia il processo produttivo vero e proprio. Il primo pezzo
realmente costruito è stato il longherone dell’ala principale, sul
quale poi si costruisce tutta la fusoliera. |
Si possono notare nel longherone i punti di
ancoraggio(fori rotondi) per il carrello retrattile tipo “infinity”. |
|
Allo stato attuale abbiamo la metà superiore della
fusoliera e stiamo lavorando per costruire la metà inferiore che
uscirà dallo stampo in un solo pezzo. |
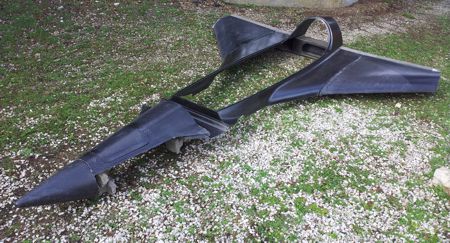 |
Il lavoro continua…… |